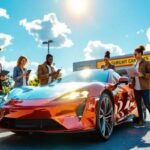
Do Shiny Roofs Sell Cars Faster Online in Tuscaloosa, AL?
December 7, 2024Powder coating is a versatile and durable finishing process used widely in industries from automotive to home appliances. But the real art of powder coating lies in the precision control of temperature inside the powder coating oven. The right temperature range ensures optimal adhesion, finish quality, and longevity for coated items. Understanding these temperature ranges—from low and mid-range to high settings—not only affects the final product but also helps to preserve the substrates and achieve specific finishes. Let’s dig into how temperature ranges influence the powder coating process and which settings work best for different needs.
Temperature Ranges in Powder Coating Ovens
Low-Temperature Curing for Sensitive Substrates
For delicate substrates, low-temperature curing is key to a flawless finish without compromising the material. Items like plastics, thin metals, or heat-sensitive components can easily warp or degrade under excessive heat, so powder coating ovens are often set to operate between 250°F and 325°F for these sensitive materials. Specialized low-temperature powders are formulated for these conditions, providing excellent adhesion while preserving the integrity of the substrate.
The advantages of low-temperature curing go beyond protection. This temperature range also allows for quicker processing times in many cases, meaning less time in the oven and a lower risk of material stress. Industries working with mixed materials especially benefit from this approach, as the controlled heat application maintains the desired finish without jeopardizing the component’s structure. This method is a win-win for manufacturers seeking durable, visually appealing finishes without high-temperature risks.
Mid-Range Heating for Standard Powder Coatings
The majority of powder coating applications fall within the mid-temperature range, typically between 325°F and 400°F. This temperature range provides a perfect balance for standard powder coatings, allowing powders to melt, flow, and cure properly to create a durable and aesthetically pleasing finish. This setting is ideal for metals, such as aluminum and steel, commonly used in automotive parts, furniture, and household appliances.
In powder coating ovens, mid-range heating is effective in achieving a consistent layer and reliable adhesion. It’s also where the highest variety of colors and textures come into play. The flexibility of the mid-range makes it a popular choice for manufacturers looking for versatility in appearance and durability. For companies focusing on efficient production and high-quality output, mid-range heating meets these needs without pushing energy costs to the limit.
High-Heat Settings for Thick or Specialized Finishes
When it comes to thick coatings or specialized finishes, high-temperature settings offer the extra power to get the job done. Temperatures upwards of 400°F are essential for thicker coatings or finishes that demand greater durability, such as outdoor furniture, heavy machinery, or marine equipment. In these cases, higher heat allows the powder to flow and settle evenly on more substantial surfaces, creating an added layer of protection against environmental factors.
Powder coating ovens operating in this high range bring a unique set of challenges. Substrates and coatings alike must withstand the heat, making material choice important. In addition, specialized powder formulas are often required to ensure compatibility. However, the results speak for themselves—high-heat settings produce finishes that are not only durable but also resistant to scratches, moisture, and UV damage. The added durability extends the lifespan of the coated items, making them suitable for tough applications.
Precision Control for Variable Temperature Requirements
In today’s manufacturing landscape, precision temperature control in powder coating ovens is crucial for ensuring product quality. Different components require different curing times and temperatures, and a reliable oven should adapt to these changing needs. Many powder coating ovens now feature programmable settings that allow operators to adjust temperatures based on the specific requirements of each batch, minimizing waste and enhancing efficiency.
The ability to control temperature precisely offers manufacturers an advantage by enabling a seamless transition from one type of coating to another. For instance, switching from a low-temperature cure for plastic parts to a high-temperature cure for metal components becomes simple and efficient. This flexibility allows companies to meet diverse project demands while maintaining a consistent and high-quality finish.
Safety Measures for Extreme Temperature Operations
Extreme temperature operations in powder coating ovens require careful attention to safety. When working with high-heat settings, operators need to consider proper ventilation, safety gear, and monitoring systems to prevent overheating. Overheating not only poses a risk to equipment but can also lead to dangerous conditions for operators if safety measures aren’t strictly followed.
Investing in temperature control systems and regular oven maintenance plays a crucial role in mitigating these risks. Fire suppression systems and temperature alarms add layers of security, while routine inspections help catch potential issues before they escalate. By adhering to these safety practices, operators can work confidently at extreme temperatures, ensuring that the coating process remains efficient and risk-free.
Balancing Ramp-Up and Cool-Down Rates for Optimal Coating
Ramp-up and cool-down rates are often overlooked yet essential elements in achieving an ideal powder coating. Ramping up the heat too quickly in powder coating ovens can lead to uneven curing or even cracking. On the other hand, a rapid cool-down can cause stress on the coating, diminishing the durability and visual quality. By carefully balancing these rates, manufacturers can enhance the consistency and longevity of the finish.
To achieve this balance, many modern powder coating ovens use programmed ramps that allow gradual temperature changes, protecting the coating’s integrity and the substrate’s stability. With controlled ramp-up and cool-down, manufacturers achieve smooth, long-lasting coatings, adding significant value to the finished products. Balancing these temperatures isn’t just a technical requirement; it’s a practical step toward achieving a superior, reliable finish that customers can trust.